同じコンセプトの搬送システム。
でも二番煎じはいやだった。
そのオファーがあった時、一部の人間にはなぜキトーに声がかかったか、わかったはずだ。「あの案件を成功させたからだな」と。10年以上も前になるが、すでに同じようなコンセプトの搬送システムに開発に携わり、成功させていたのである。航空機ジェットエンジンの整備工場内で、エンジンをホイストで吊り上げたままメンテナンス作業ができるようにした搬送システムである。9t ものジェットエンジンをクレーンで吊り上げて移動させ、ユニットを次々と分解しながら進み、今度はメンテナンスされたユニットを次々と組み込みながら戻ってくる。つまりエンジンは一度も地上に降ろされることなく整備されることになるわけだ。
ユニットごとに床に置いて作業をしていた従来の発想と180度逆転させたシステムと言えるが、この場合、当然のことながらエンジンを吊り、移動させるホイストやクレーンがきわめて重要な役割を持つことになる。当時、メンバーの一人であった中村賢三によれば、「国内初という野心的な搬送システムでしたが、クレーンとホイストの評価の高かったことが再びオファーのあった理由でしょう」。国内でキトーの評価にはゆるぎないものがあるとは言え、同じようなシステムを開発した実績があるというのは大きな意味を持つ。こうした経緯から、別の航空会社の整備工場であっても、キトーが指名されたのだろう。しかし、同じコンセプトであっても以前の搬送システムと同じであってならないことは言うまでもない。エンジニアであれば誰だって「二番煎じではダメだ。もっと進化させたシステムとして結実させたい」と願うだろう。キトーにおいても例外ではなかった。
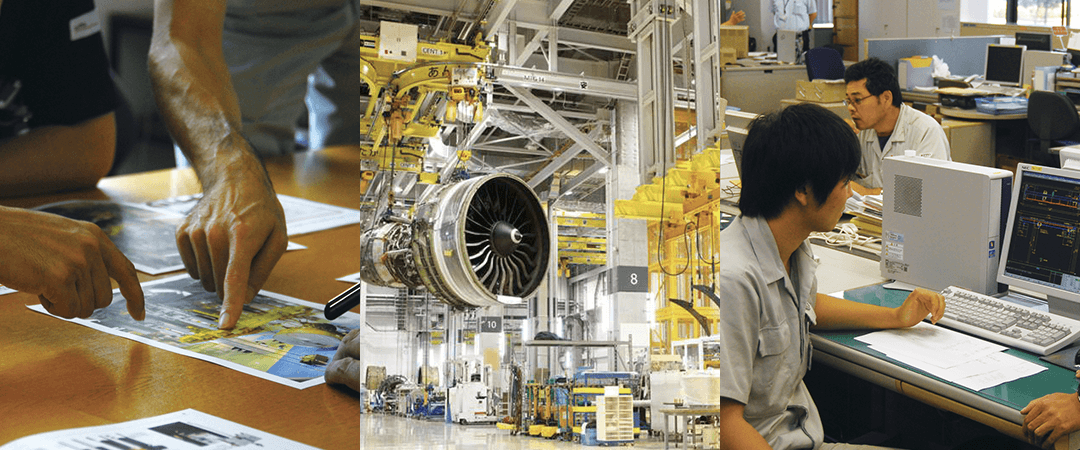
スケールとセンシビリティの
両方が求められたプロジェクトだった。
中心となったメンバーは塩澤英明をリーダーとして6人。ホイスト設計の中村と藤井視弘、クレーン設計の望月浩行と甘利美英、小林義正、生産技術の柳原伸章である。しかし、いきなりプロジェクトは壁に当たることになる。以前のシステムではジェットエンジンをターンさせる際、ターンテーブルを採用していたのだが、スペースの関係上、それが難しいことがわかったのだ。「ターンテーブルだとターン後、エンジンの向きが変わってしまい、作業性に影響が出ることも懸念されました」。悩んだ塩澤が選んだのはスイッチバック方式だったが、すでにこの段階で新しい設計に挑戦しなければならないことになった。
ホイストが約160台、レーンから別のレーンへの乗り移り場所が60ヵ所にも上ったクレーン設計だが、コンマミリ単位での精度が求められた。甘利や望月たちが声をそろえて強調したのは「ジェットエンジンは精密機械。落ちることがあってはならず、乗り移りをスムーズにするためにもクレーン同士の精度を十分に確保する必要がありました」。300m近くにも及ぶ整備工場の中で走るクレーンだから、設計作業は膨大なものになる。その一方で作業の効率性や安全性を保証するための緻密な精度管理が求められる。まさにスケール感とセンシビリティが同居したプロジェクトであった。
電気制御でも新しい試みが始まっていた。それまでの有線式の多重伝送装置に代えて、光伝送装置、無線装置を使ったシステムの採用を決めたのだ。システムのシンプル化、コストダウンを考慮してのことだが、必然的にセンサーの数が増え、ここでも設計が苦労することになる。藤井によれば「使われたセンサーの総数は従来とは桁外れの100個以上。その位置を決めていくだけでも大変でした」。センサーの位置を変えれば、それをハード設計に反映させていかなければならない。ハードとソフトの連携が不可欠になってくるわけで、このために電気制御を担当した藤井は中村や小林と何度も意見を交換することになる。最終的にこうした努力は実を結び、キトー独自の特許技術として認められたのだが、このプロジェクトではさらに安全確保のためのストッパー機構でも特許を取得することになった。
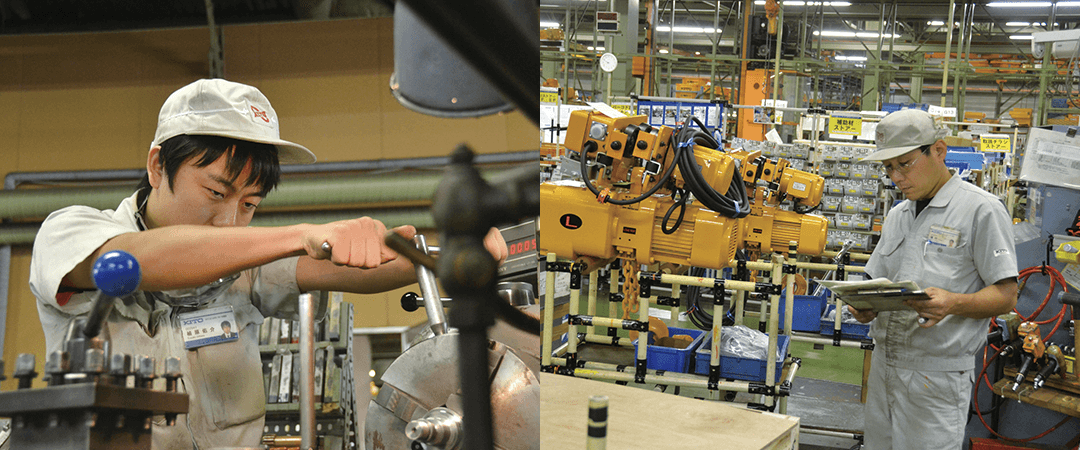
お客様は満足を求めるから
設計変更を依頼してくるんだ。
これだけ大きなプロジェクトになると製造はもちろん、部品や資材の手配も膨大な作業になることが予想された。そこで部品手配と納期管理を担当した柳原の挑んだのが、部品表のデータシステム導入だった。「部品の種類で2,000、点数で約10万点と、膨大になることが最初からわかっていたので導入に踏み切りました。もし、やらなかったら? 多分、納期は大幅にズレていたでしょう」。通常の手配だけでも大変だが、それに設計変更が加わると、管理はさらに大変なことになる。新たな部品の手配や納期の変更などを余儀なくされるわけで、それでもこのシステムのおかげでずいぶんとスムーズにいったと柳原は振り返る。
プロジェクトは問題を抱えながらも着実に進んでいったが、この過程の中で一番彼らを悩ませたのは、先にも触れた設計変更の多さである。たとえば、当初の予定ではA→Bと乗り移る予定だったものが、お客さまの作業手順に変更が出てB→Aと反対になるといったことだ。「それに対応するには仕様をすべて見直さないといけない。たくさんのホイストやクレーンが電気制御で連携して動くわけですから、ちょっとした変更でも全体に大きな影響を及ぼしてしまう」と小林。その対応にかなりの時間を割かなければならなかったのだ。納期が迫る中で、設計変更に対応しつつ設計・製造・現場搬入を進めなければならない。時間との闘いだから、お客様から変更依頼が来ると「いい加減にしてくれ」と心で叫ぶことも少なくなかったという。
設計変更に追われるプロジェクトメンバー。塩澤はそうしたメンバーを見ながら気軽に声をかけ、粘り強く励ましていたが、一方で「プロジェクトでは設計や仕様の変更といったトラブルがあるのは当然」との思いも抱いていた。「お客様は満足を求めるからこそ変更を頼んでくるんだ」。やがて、この考えは徐々に他のメンバーにも伝わっていき、「だったら、満足と感動を提供したいキトーがそれに応えるのは当然ではないか」という思いを誰もが共有するようになっていった。
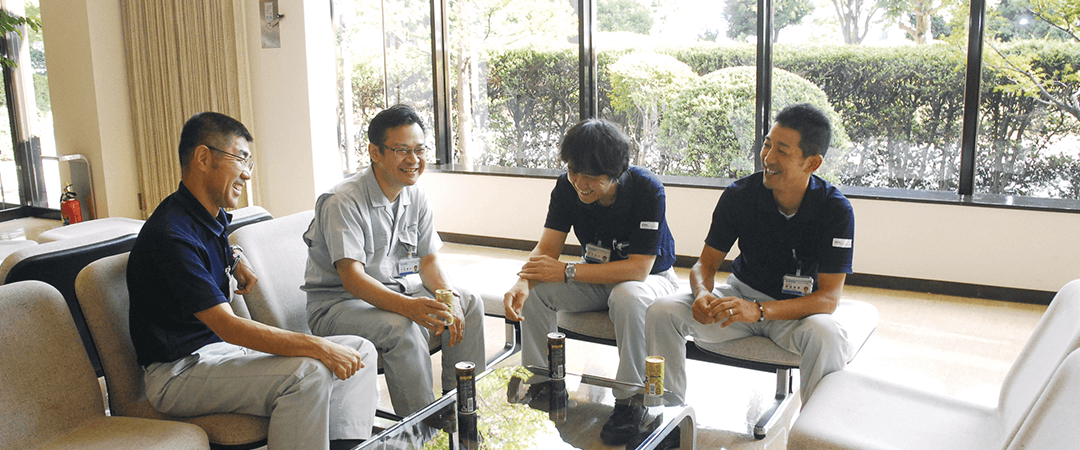
できるかどうかではなく、
どうすればできるのかを考える。
オファーを受けて全体的な仕様の打ち合わせや見積もり作業を進め、受注になるまでに約2年。それから本格的な設計作業や製造にかかってから1年。完成した機器が次々と運び込まれ、現地でシステムが徐々に組み上がっていく。現場に立ち会った者が例外なく圧倒されたのは、スケールの大きさだった。小林が言うのは「自分が図面に引いた一本の線が、実際にはいかに大きいものであるか、改めて実感できた」。そして、試運転の日。巨大な航空機ジェットエンジンはプロジェクトメンバー苦心のクレーンに吊り上げられ、静かに“離陸”していった。
紆余曲折がありながらも、これだけの大きなプロジェクトがなぜ成功したのか。メンバーが一致して強調するのはメンバー同士のコミュニケーションの良さである。エンジニア同士いつでも気軽に情報交換できる環境にあるし、営業や建設会社のスタッフを交えたミーティングも頻繁に行った。加えて、キトーらしさにあふれたポジティブ発想によるところも大きかったと塩澤が言う。「できる、できないで判断するのではなく、どうすればできるのか、できるようにするためには何が必要かを考えるという発想です」。
かつてないスケールの仕事することで、これ以降、どんな案件が来ても動じなくなったこと、「お客様は満足を得たいから変更を言ってくる。だったらそれに応えてあげるのは当然」と思えるようになったこと、そして、「できる、できないではなく、どうしたらできるのか」という発想の大切さを学んだこと。このプロジェクトがメンバーたちに残したものは少なくないようだった。
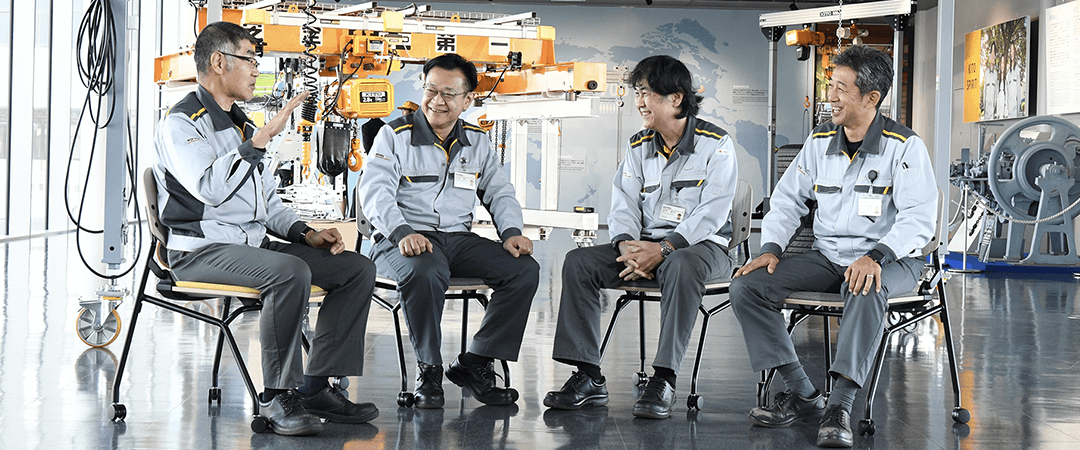
4名のメンバーが再集結し、当時を振り返る